SMT制造你需要知道的全部
發(fā)布時間2023-04-09 20:37:19
簡介
表面貼裝技術(shù)(SMT)是電子制造的一個方面,在這個過程中,電子元件,也稱為表面貼裝器件(SMD),直接安裝在印刷電路板(PCB)的表面上。由于其成本和質(zhì)量效率,SMT在行業(yè)中變得備受追捧。什么是表面貼裝技術(shù)(SMT)? 表面貼裝技術(shù)(SMT)是一種裝配和生產(chǎn)方法,將電子元件直接應(yīng)用到印刷電路板(PCB)的表面上。這個過程允許自動化生產(chǎn)完成更多所需的組裝工作以創(chuàng)建一個工作板。通過這種方法安裝的任何電氣元件都被稱為表面貼裝器件(SMD)。與傳統(tǒng)裝配不同,SMT不需要將元件插入孔中,而是直接通過回流焊接將元件焊接在板上。
最初被稱為平面安裝技術(shù)(Planar Mounting),SMT在1960年代由IBM首次開發(fā)和應(yīng)用于構(gòu)建小型計算機(jī),成為其前身——插針式技術(shù)的替代品。不過,直到1986年表面貼裝元件實現(xiàn)10%的市場份額時,SMT才開始起飛。到了1990年,表面貼裝元件或SMD已經(jīng)可以在絕大多數(shù)高科技印制電路組件(PCA)中找到了。
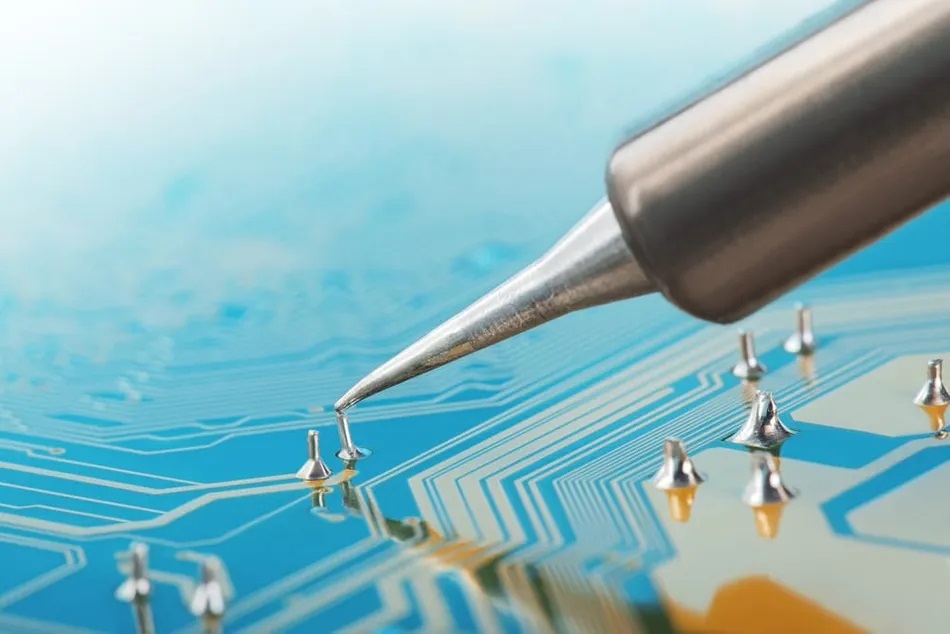
SMT組件設(shè)計成有小選項卡,焊錫可以應(yīng)用于將SMD附加到PCB的表面上。在插針式技術(shù)時代,成分通過在PCB上鉆孔得到裝配。孔的大小設(shè)計成適合每個成分以將每個零件緊密地固定,然后用熔融的氧化鉛進(jìn)行鍍錫以固定。目前SMT中孔鉆的過程被繞過,因為SMD可以快速進(jìn)行分類并附加到PCB的頂層,幾乎不需要鉆孔的引腳。這顯著縮短了設(shè)備組裝的過程。
如果手動完成,由于需要準(zhǔn)確度來創(chuàng)建高質(zhì)量的表面貼裝組件(SMA),表面貼裝裝配過程可能會很麻煩且耗時。因此,在大規(guī)模生產(chǎn)時,大多數(shù)SMT制造都是通過自動化裝配機(jī)器完成的,以提高效率。
SMT組件比插針式組件顯著小一些,這使得生產(chǎn)適合現(xiàn)代時代的時尚和有吸引力的電子設(shè)備變得容易。因此,現(xiàn)在SMT被廣泛應(yīng)用于從玩具到廚房電器,再到筆記本電腦和智能手機(jī)等幾乎每個電子設(shè)備中。
SMT制造過程
SMT制造過程被廣泛分為三個階段,即:焊膏印刷、元件安裝和回流焊接。由于SMT生產(chǎn)過程的要求,這些階段在以下概述中得到了進(jìn)一步分析:1.SMC和PCB準(zhǔn)備
這是在SMCs進(jìn)行選擇和PCB設(shè)計的初步階段。該板通常包含平坦的、通常是銀色、錫鉛或鍍金的無孔銅墊片,稱為焊墊。焊墊支撐元件的引腳,如晶體管和芯片。另一個重要的工具是模板,用于根據(jù)PCB上焊墊的預(yù)定位置,為下一階段的過程(焊膏印刷)提供固定位置。這些材料以及制造過程中使用的其他材料必須進(jìn)行適當(dāng)?shù)臋z查。
2.焊膏印刷
這是SMT過程中的關(guān)鍵階段。在這個階段,印刷機(jī)使用預(yù)制模板和擠壓板(用于印刷中清洗的工具)以45°至60°的角度應(yīng)用焊膏。焊膏是一種由金屬焊料和粘性助焊劑組成的膏狀混合物。助焊劑用作暫時膠水,以將表面貼裝元件固定在位置上,并清潔含氧和雜質(zhì)的焊接表面。另一方面,焊膏用于連接SMC和PCB上的焊墊。很重要的是,每個焊墊都要涂覆正確數(shù)量的焊膏。否則,當(dāng)在回流爐中熔化焊料時,就不會建立連接。在電子制造行業(yè)中,回流爐是一種用于將電子元件放置在印刷電路板(PCBs)上的電子加熱設(shè)備,用于表面貼裝技術(shù)(SMT)。
3.組件安置
接下來,使用拾放機(jī)在 PCB 上安裝組件。每個組件使用真空或夾爪噴嘴從其包裝中取出,并將其放置在其設(shè)計位置。 PCB 被運(yùn)送在傳送帶上,同時電子元器件由快速準(zhǔn)確的機(jī)器放置在上面,其中一些機(jī)器可以每小時放置 80,000 個單獨(dú)的組件。在這個過程中需要精度,因為放錯位置的元器件會導(dǎo)致昂貴和耗時的重新修復(fù)。
4.熱風(fēng)焊接
在 SMC 被放置之后,PCB 然后被傳送到回流焊接烤箱中,其中經(jīng)過以下區(qū)域以進(jìn)行焊接過程:預(yù)熱區(qū):這是烤箱中的第一個區(qū)域,其中板和所有附加的元器件的溫度同時逐漸上升。溫度以每秒 1.0℃-2.0℃ 的速率增加,直到進(jìn)入 140℃-160℃。
浸泡區(qū):在這里,板將保持在 140℃ 和 160℃ 之間的溫度下 60-90 秒。
回流區(qū):然后,板進(jìn)入一個區(qū)域,該區(qū)域的溫度以每秒 1.0℃-2.0℃ 的速率升高到最高 210℃-230℃,以融化焊膏中的錫,將元件引線焊接到 PCB 上的墊片上。在此過程中,通過熔融焊料的表面張力來保持元件的位置。
冷卻區(qū):這是最后的部分,確保焊料在離開加熱區(qū)后凍結(jié),以避免接頭缺陷。
如果印刷電路板是雙面的,則可以使用焊膏或膠水重復(fù)這些過程,以保持 SMC 的位置。
5.清洗和檢查
焊接后,電路板將被清洗并檢查是否存在缺陷。如果發(fā)現(xiàn)任何缺陷,就會修復(fù)這些缺陷,然后將產(chǎn)品存儲。用于 SMT 檢查的常見方法包括使用放大鏡、自動光學(xué)檢測、飛針測試儀、X-ray 檢測等。 機(jī)器代替肉眼進(jìn)行有效快速的結(jié)果。SMT:優(yōu)點(diǎn)和缺點(diǎn)
SMT 已經(jīng)在 PCB 組裝 (PCBA)、PCB 制造和電子生產(chǎn)等方面證明了許多好處,包括:
允許更小的組件。
SMT 過程鼓勵增加自動化。
在構(gòu)建 PCB 時具有最大的靈活性。
性能和可靠性提高。
減少了用于元件擺放的人工干預(yù)。
板子更小,更輕。
使用傳統(tǒng)方法所存在的孔的限制之外,更容易組裝 PCB,同時使用板的兩側(cè)。
即使在同一板上,可以與通孔元件共存。
相同空間內(nèi)具有更多的 SMD 組件,或者在更小的框架中使用相同數(shù)量的組件,從而提高了密度。
材料成本低廉。
簡化了生產(chǎn)過程,降低了生產(chǎn)成本。
相反,SMT 對電子制造的不利影響包括:
小規(guī)模的生產(chǎn)。
易于因脆弱而破裂。
對焊接技術(shù)有高要求。
安裝組件時很容易掉落或損壞。
非常難以進(jìn)行目測檢查。
由于微型化和數(shù)量眾多的焊接點(diǎn)類型,使得過程和檢查變得更加復(fù)雜。
需要大量投資于設(shè)備,如 SMT 機(jī)器。
技術(shù)復(fù)雜性需要高的培訓(xùn)和學(xué)習(xí)成本。
快速發(fā)展需要持續(xù)跟進(jìn)。
SMT vs SMD SMT 和 SMD 經(jīng)常被誤解并同時使用。實際上,任何技術(shù)及其實際組件都可以深度交織,從而造成混亂。這就是 SMT 和 SMD 的情況。因此,了解 SMT 組裝和單個 SMD 元件之間的區(qū)別非常重要。
簡單來說,SMT 是技術(shù)中的過程,而 SMD 是技術(shù)中涉及的設(shè)備。SMT 是一種使用將電子元件直接放置和焊接在 PCB 上的方法的技術(shù)。這些元件有時也被稱為表面貼裝器件或 SMD。它們被設(shè)計成安裝在印刷電路板 (PCB) 上。
SMD 構(gòu)件使得設(shè)備生產(chǎn)更快、更靈活和成本更低,而不會犧牲功能性。它們承諾提供更多的功能性,因為更小的元件允許在較小的板空間上實現(xiàn)更多電路。這種微型化是 SMD 的主要特點(diǎn)。
SMT 和 SMD 一起工作,為用戶提供更快、更節(jié)能和更可靠的 PCB。
更小的尺寸、更快的生產(chǎn)速度和更輕的重量是 SMT 的主要吸引力,從而導(dǎo)致電子電路設(shè)計和生產(chǎn)變得更加容易,尤其是在復(fù)雜電路中至關(guān)重要。這種更高水平的自動化在整個電子制造業(yè)中節(jié)省了時間和資源。因此,即使存在開發(fā)新技術(shù)的可能性,SMT 無疑已經(jīng)確立了其相關(guān)性。